Introduction:
A Hydrostatic slide is non-contact in that the slide is supported by a film of high pressure oil, in the order of 10 Um. It functions by producing a continuous flow of high pressure oil through and out of the bearing. The flow rate being controlled by restrictors. The restrictors allow the slideway to cope with varying loads and maintain a near constant film thickness. Throughout the bearing surface, small pockets or pads are machined to create areas of high pressure fed by these restrictors and from which the oil flows ,to the rest of the bearing surfaces before exiting the bearing. The oil is then collected, filtered, repressurized, and recirculated. [Handbook, pg. 294]
ANANT JAIN
(M2G) Machining to Grinding [1]
Introduction:
Spiralling costs, global competition, and the green movement are just a few of the many pressures manufacturers are now facing. Many manufacturers are being forced to become more innovative on how best to process parts and reduce total manufacturing costs. Additionally, changes in part requirements have also brought new challenges. High-heat-resistant materials, improved strength-to-weight ratios, tighter tolerances, and finer surface finishes have challenged traditional methods of machining. These stresses have created a demand to provide total cost solutions by developing new approaches.
Machining to Grinding (MTG) is the conversion of a high-scrap, high-cost machining operation to a stable, low-cost, and high-quality grinding application [2]. Recent advances in abrasive cutting tools and the shift in material properties have allowed grinding to achieve the low Specific Cutting Energy and high Material Removal rates typically observed in machining operations, making the M2G process technically feasible and economically attractive. Advantages of the M2G process can be:
-
Comparable or better size tolerances as compared to machining
-
Better Surface finish due to the presence of random cutting edges
-
Soft Machining can be totally eliminated in case of through hardened components reducing the no. of manufacturing processes
-
Issues such as tool wear and break down can be completely avoided
Need
The major requirement of the project was to develop a grinding machine and implement an M2G solution for kneading block elements.
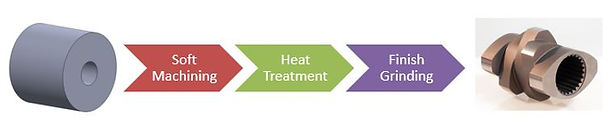

Advantages foreseen
-
Lesser No. of Manufacturing Processes
-
Faster Cycle Times
-
Avoidances of issues associated with tool failure and breakage
-
High Profile accuracy and finish
-
Reduced total cost per component
Project Definition and Organization
The Project has been organized as a Unique New Solution or a UNS project to be executed with the systems approach. My major role as the project manager was to see the project from concept to commercialization. The project was divided into the following clusters:
-
Economic Feasibility:
-
Evaluate the commercial feasibility of the project and arrive at the required CPC (cost per component) for the project to be commercially viable
-
-
Technical Feasibility Study:
-
Derive the required technical conditions such as MRR (material removal rate) and G-ratio (a metric of wheel life) to achieve the above CPC, literature review to compare the derived values with standards achieved
-
-
Grinding Process:
-
Process Kinematics to achieve the desired component profile
-
Grinding process is a combination of 6 microscopic interactions, the versatility of the process lies in the fact that these 6 interactions can be manipulated by suitably modifying the inputs such as abrasive wheel etc. The challenge here was to identify how these tribological interactions should be manipulated to achieve required wheel life while removing 30 times the amount of material traditionally removed in grinding
-
-
Machine Design:
-
Basic machine design and layout
-
Selection of sub-assemblies for high stiffness and thermal stability
-
Development of in-feed slide capable of rapid oscillation; the in-feed slide has to oscillate to trace the non-round shape of the component. The productivity may get limited by the slow movement of the in-feed slide. This was addressed by:
-
Using Hydrostatic slide in lieu of traditional roller bearing slides due to their low friction
-
Using Linear Motor in lieu of traditional ball screw mechanism; the former provides benefits in terms of high speeds, low inertia, zero back-lash and pitch error among others
-
-
-
Software Development:
-
Development of the software with GUI package which will run on industrial PC on the machine
-
It will act as a “pre-processor” and interfaced with the CNC system for machine control
-
Function pf pre-processor:
-
Loading/ Generating Non-Round Profiles
-
Reading machine conditions from CNC such as wheel diameter, offset values etc.
-
Generation of feed-profile and CNC code
-
-
-
Integration testing and part prove-out
-
Integration between sensors (such as acoustic and proximity), CNC and software
-
Proving out quality and cycle time requirements for various components
-
Accomplishment
-
Integration of low friction Hydrostatic slide into a grinding machine
-
Insert a picture of Linear Motor integrated onto a slide
Integration of Linear motor onto a grinding machine which was done for the first time in MGT. Linear motors offer advantages in terms of low inertia leading to high speeds and acceleration, at the same time linear motors exert extremely high magnetic force around 22kN making the design and assembly extremely critical
-
Certain tasks such as machine referencing which is traditionally done manually has been automated through integration of various sensors, for the first time in MGT
-
Pre-Processor GUI on a grinding machine was developed for the first time in the company
-
The project has led to commercial impact for the company in terms of the most expensive machine sold by the company so far
Major areas of learning
-
Converting Customer Needs into Design Specification:
-
Studying and analyzing customer’s production and batch sizes
-
Evaluating economic feasibility of the project
-
Establishing machine features required to meet the needs of the customer
-
-
Grinding Process
-
Creep feed Grinding
-
State of the art for Machining to Grinding
-
Microscopic Interactions in a Grinding Process and how to manipulate them
-
-
Machine Design and Assembly
-
Criticalities of assembling hydrostatic slide and linear motors
-
-
CNC Systems:
-
G-code programming
-
Feed-forward and learning control
-
Setting up CNC communication for retrieving and transmitting data
-
References
[1] Subramanian K., Babu N. R., Jain A., Vairamuthu R., "Microscopic Interactions in Surface Generation Processes using abrasive tools, " Journal of Manufacturing Science and Engineering, vol. 139, Issue -12, Nov. 2017
[2] P. Baliva, “Converting Machining Applications to Grinding,” Manufacturing Engineering, February 2009