Introduction:
A Hydrostatic slide is non-contact in that the slide is supported by a film of high pressure oil, in the order of 10 Um. It functions by producing a continuous flow of high pressure oil through and out of the bearing. The flow rate being controlled by restrictors. The restrictors allow the slideway to cope with varying loads and maintain a near constant film thickness. Throughout the bearing surface, small pockets or pads are machined to create areas of high pressure fed by these restrictors and from which the oil flows ,to the rest of the bearing surfaces before exiting the bearing. The oil is then collected, filtered, repressurized, and recirculated. [Handbook, pg. 294]
ANANT JAIN
Grinding Process Solutions
Introduction
GPS aims to provide significant improvements in existing manufacturing processes by integrating manufacturing knowledge with a scientific basis (cause/effect based on the physics of the process) through a System Approach and through the use of MGT’s proprietary diagnostic tool Grind-TrakTM developed with support of Dr. K. Subramanian of STIMS Institute USA.
Project Organization
We work as a small expert team under Dr. K. (Subbu) Subramanian‘s guidance, to carry out the projects under GPS. The projects of GPS come under the purview of “value selling” and therefore require the buy-in of the high-level management of the client.
After the initial interaction of the top-level management, the lead is handed over to the GPS team. The major activities are:
-
Preparation of the proposal
-
Understanding the customer requirement
-
Preliminary documentation
-
Estimating the value of the project to the customer
-
Making the proposal
-
Internal Review
-
Submitting the proposal
-
Customer Approval – Deliverable, time-line and cost
-
-
Project Execution:
-
Diagnostics
-
Detailed system documentation
-
Grind-Trak studies
-
Capturing other process and quality data
-
Analysis of the in-process signals
-
Recommendations for solution (incorporating customer constraints)
-
-
Implementation
-
Implementation of the solutions
-
Documentation of the impact of the solution
-
-
Project Report and Closure
-
Making the report
-
Agreement of scope completion
-
Project closure
-
Personal Contributions and Accomplishments

Grind-Trak: A portable diagnostic tool commercialized by MGT
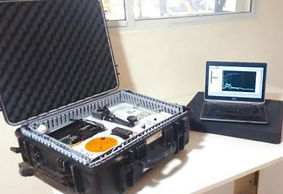
I have been part of a 2 member team which has been involved in 2 GPS projects:
Case Study 1:
-
Problems faced: The customer had reported problems of low productivity and frequent component rejection (due to size variation), for an external cylindrical grinding process
-
Process Modification: The GPS captured the in-process signals, performed the analysis and modified the process parameters to address the above 2 problems:
-
The cycle time was reduced by increasing the MRR and removing the non-grinding time
-
The process parameters were changed to reduce the grinding power (and in turn grinding forces) to tackle the problems of size variation
-
-
Accomplishments:
-
Productivity improvement by 25% and rejection Reduced by 80%
-
This was a paid service resulting in commercial impact for the company
-
Grinding Machine Power Signals for previous and modified cycle captured through MGT's proprietry diagnostic tool Grind-Trak

Commercialized version of grind-trak assembled as a product ready kit
Case Study 2:
-
Problems faced: The customer desired an increase in productivity for an internal grinding process
-
Process Modification: The GPS team captured the in-process signals, performed the analysis and modified the process parameters to address the problem of low productivity. The cycle time was reduced by optimizing the slide movement and increasing the material removal rate during grinding
-
Accomplishments:
-
Productivity improvement by 37%
-
New Customer acquisition
-